INVENTORY AND SUPPLY MANAGEMENT SOFTWARE
Poor inventory management leads to stock-outs and extra costs. Without a centralized tool, multi-channel management becomes complex. Our solution offers real-time inventory management, with a unified view to reduce inventory, avoid stock-outs and improve service.
- Better visibility, anticipation, coordination and management
- Financial gains through reduced inventory, less breakage and increased availability.
- Productivity gains through process automation and ease of use
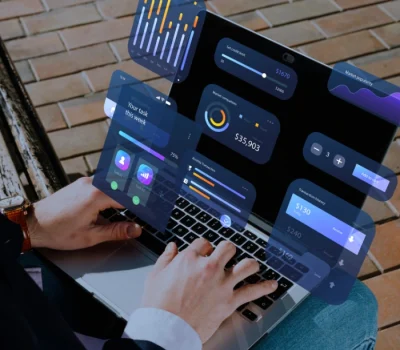
THEY TRUST US
Supply chain optimization: a strategic lever for supply chain performance
In an omnichannel environment, where customer expectations and supplier constraints are constantly evolving, procurement is no longer a simple operational task: it’s a key pillar of profitability and customer satisfaction.
Yet many companies still operate with compartmentalized systems, rigid rules or poor inventory visibility, risking stock-outs, additional logistics costs or late decisions.
Implementing an intelligent procurement solution means equipping yourself with the means to smooth flows, manage inventories in real time, and align business objectives with operational constraints thanks to consolidated, shared and actionable data.
Why is optimizing procurement essential?
Optimized management of safety stock ensures better service rates, particularly for fast-moving items.
Avoiding excess stock reduces storage costs, breakage and wastage, while improving product rotation.
The centralization of multi-site and multi-level data provides a unified vision, essential for coordinating stores, platforms and e-commerce.
The integration of supplier constraints, allocation rules and stock projections enables rapid adaptation to unforeseen circumstances.
Order suggestion, requirements calculation and data visualization reduce manual workload and improve operational responsiveness.
Less waste, less unnecessary transport, better rotation: optimized supply management has a direct impact on the environmental footprint.
Your procurement decisions deserve better than approximations.
Thanks to our inventory and supply optimization solution, you have a complete tool for anticipating demand, securing your stock levels and rationalizing your flows – with complete agility, across all your channels.
A tried-and-tested methodology for managing your product-site procurement
At a time when logistics costs are soaring and every square meter of storage space counts, an inventory management and optimization solution enables you to control your stock levels with precision.
It’s a direct lever for improving profitability, boosting product availability and making your omnichannel operations more reliable.
1. SAFETY STOCK OPTIMIZATION
The module calculates the minimum stock level to avoid shortages, taking into account uncertainties (demand, supplier constraints, lead times, order frequency, etc.).
2. PROJECTION CALCULATION
The module also calculates stock projections, orders, shortages, breakages, etc...
3. ORDERING SUGGESTION
Calculation of initial requirement, synchronization and integration of grouping, with management in stock position. Integration of smoothing constraints if necessary.
4. ALLOCATION
Possibility of push flow of products at risk (supplier shortages, best-before date, etc.) with configurable distribution rules.
Our customers are our first ambassadors
The tool perfectly meets our users' expectations, thanks to total transparency in its operation and configuration. Its management by exception and its "typical week" approach have enabled us to optimize our forecasts and supplies efficiently.
What's more, integration into a standard ensures the stability and ongoing evolution of the solution, while respecting project deadlines and costs.
Thanks to the optimix solution, we have not only reduced the number of errors, but also maximized our analysis capabilities, in particular for segmenting our competitors (BtoB, BtoC, etc.). Our business teams managed to halve their alignment time, with increased productivity: over 12,000 products linked in just 3 minutes. The solution is complete and covers our needs 360 degrees. The tool is ergonomic and price management is simplified.
My experience of using the Optimix solution and working with the teams has been very positive.
The software has significantly improved our pricing decisions, thanks to accurate information. We have benefited from a solid relationship with the Optimix teams, and the rapid deployment in 6 months has reinforced our confidence in this successful collaboration.
THESE PLUS
THAT MAKE ALL THE DIFFERENCE
Reduced stock-outs → Increased salesFewer products missing from shelves or online, so more sales.
Reduced inventory→ Improved cash flowLess tied-up capital and better inventory turnover.
Improved product availability → Better customer satisfaction The right products, in the right place, at the right time, for a seamless customer experience.
Modules designed to manage your entire supply chain from A to Z
All your supply chain needs in one integrated APS solution
Sales forecasts and AI
Generate accurate forecasts thanks to machine learning algorithms that integrate historical data, seasonality and exogenous signals. Gain decision-making reliability over all your planning horizons.
Orders Projections
Accurately project your net supplier order requirements. Visualize the impact of purchasing decisions on your future inventories, and secure your relationship with suppliers.
Delivery flow management
Optimize your delivery flows by anticipating receiving capacities and coordinating shipments. Reduce costs and ensure reliable, on-time deliveries.
Want to optimize your inventory? Contact us !
FAQ
Optimization of inventory and procurement
1. Why is inventory management so important?
Good inventory management helps to avoid stock-outs, reduce costly overstocking, streamline the supply chain and improve customer satisfaction. It has a direct impact on your profitability and operational efficiency.
2. How does your solution differ from a traditional ERP?
Our solution specializes in advanced stock optimization: it integrates predictive modules, intelligent recommendations, dynamic To Do Lists and management by exception to go far beyond simple ERP logistics tracking.
3. Who is our solution for ?
It is aimed primarily at retail chains in the business verticals below:
- Distribution & Retail
- Food industry
- E-commerce & Omnichannel
- Industry & Manufacturing
- Pharmacy & Health
- Fashion & Textiles
- DIY, Garden & Home
- Cosmetics
- Consumer electronics
- Professional supplies & equipment
4. Is it suitable for multi-site companies or retailers?
Yes, the solution manages several million product/site references, with customizable interfaces for each user profile (stockist, category manager, merchandiser, etc.).
5. Can restocking be automated ?
Absolutely. Our modules automate restocking based on actual demand, supplier lead times and defined logistics parameters. This reduces errors and optimizes costs.
6. What is safety stock and how can it be optimized?
Safety stock is a strategic reserve to avoid stock-outs. Our tool automatically calculates it by integrating key factors such as demand, delivery times and target service rate.
7. How visible is my inventory in real time?
You have a centralized dashboard with customized views, real-time alerts and a clear view of your stock levels, future needs and priority actions.
8. Does the tool take into account the minimum presentation requirements?
Yes, our solution integrates point-of-sale presentation constraints to guarantee optimal product visibility, without compromising stock optimization rules.
9. What are the concrete short-term benefits?
Reduced out-of-stocks, better product availability, lower overstocking, time savings for teams, easier decision-making and improved sales.